Gloverall has hit the OPUMO pages just in time for the colder months, it’s almost as though it was planned. We like to give new brands a welcome to the platform when they first arrive, so you can consider this a formal welcome to Gloverall; we also like our readers to be confidently acquainted with our brands. We thought we’d try to combine both of those desires in just one article with the help of Marianne, the head of design at Gloverall.
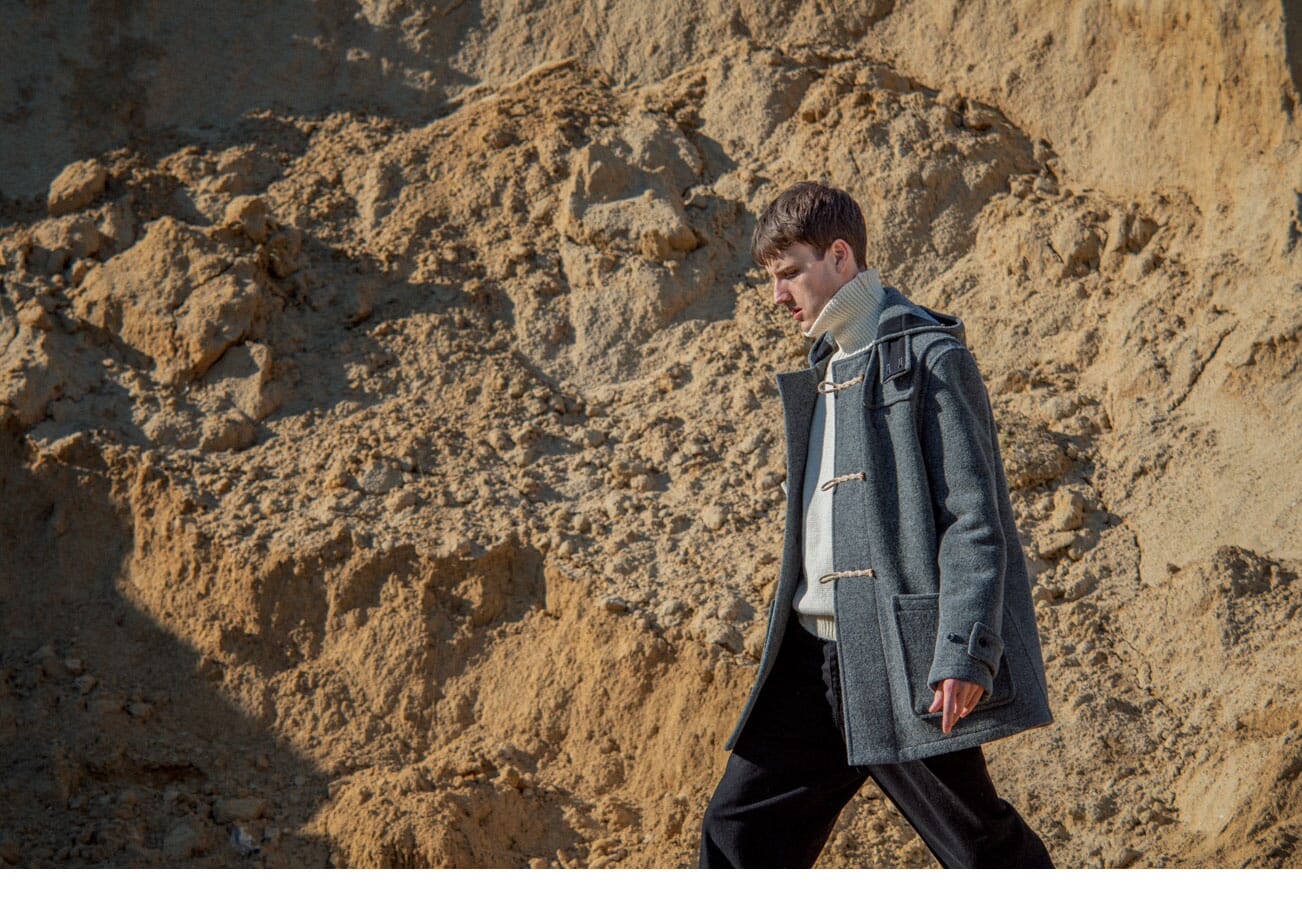
From drawing board to Gloverall rails, a design goes through a lengthy journey, passing through many hands and many different skillsets on its way to earning a Gloverall label. In our new series: How We Work, we want to delve deeper on this process, finding out what it really takes to produce items to the standard we’re used to at OPUMO.
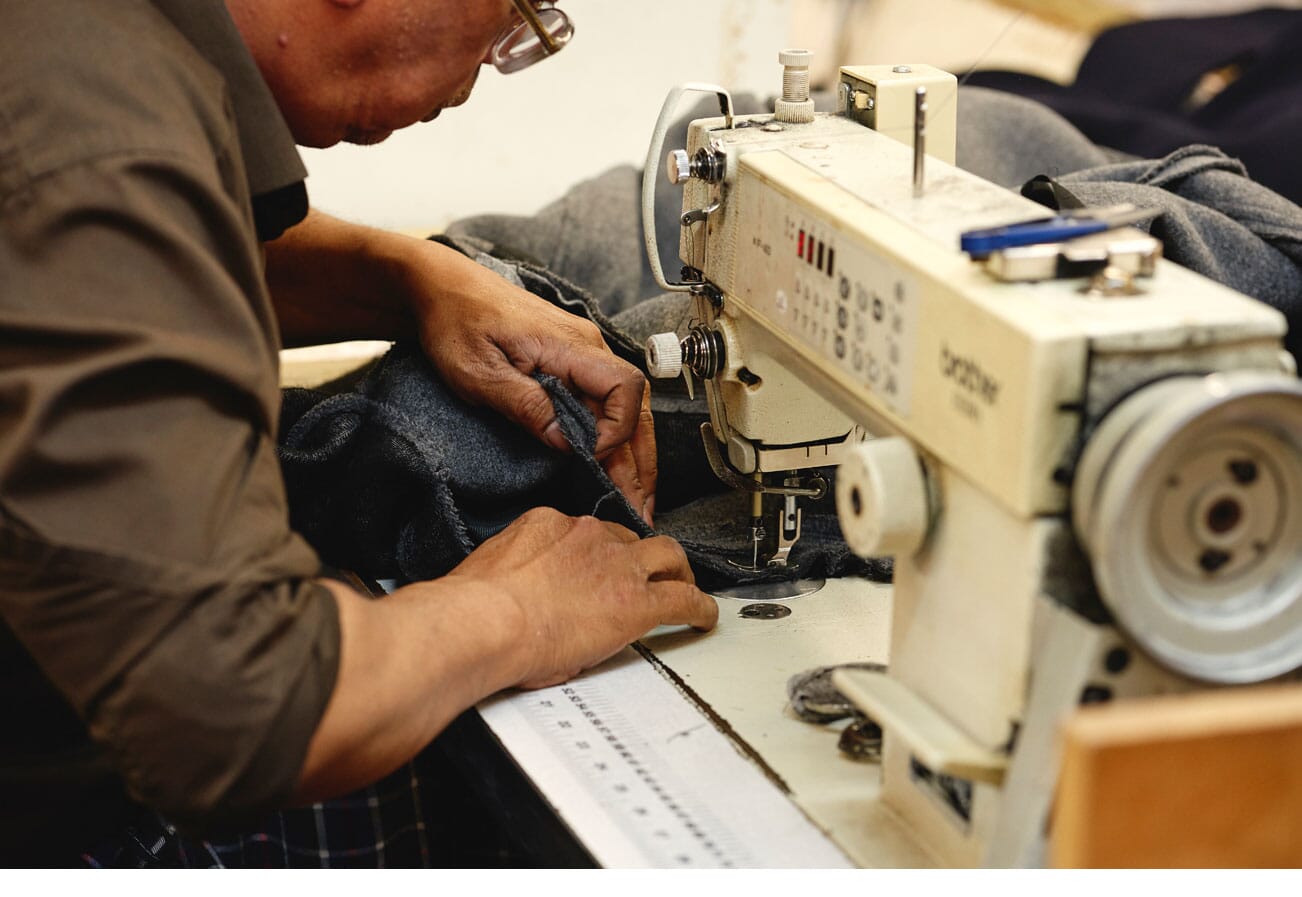
How and where do you gain inspiration?
Up in our Northamptonshire office, we have a Gloverall archive that dates back to when the brand started in 1951. I also look into military garments as this is the real foundation of the brand and it’s something that has to be considered to ensure each item stays true to our style. We tend to stay away from being too trend-driven and influenced by fast fashion markets.
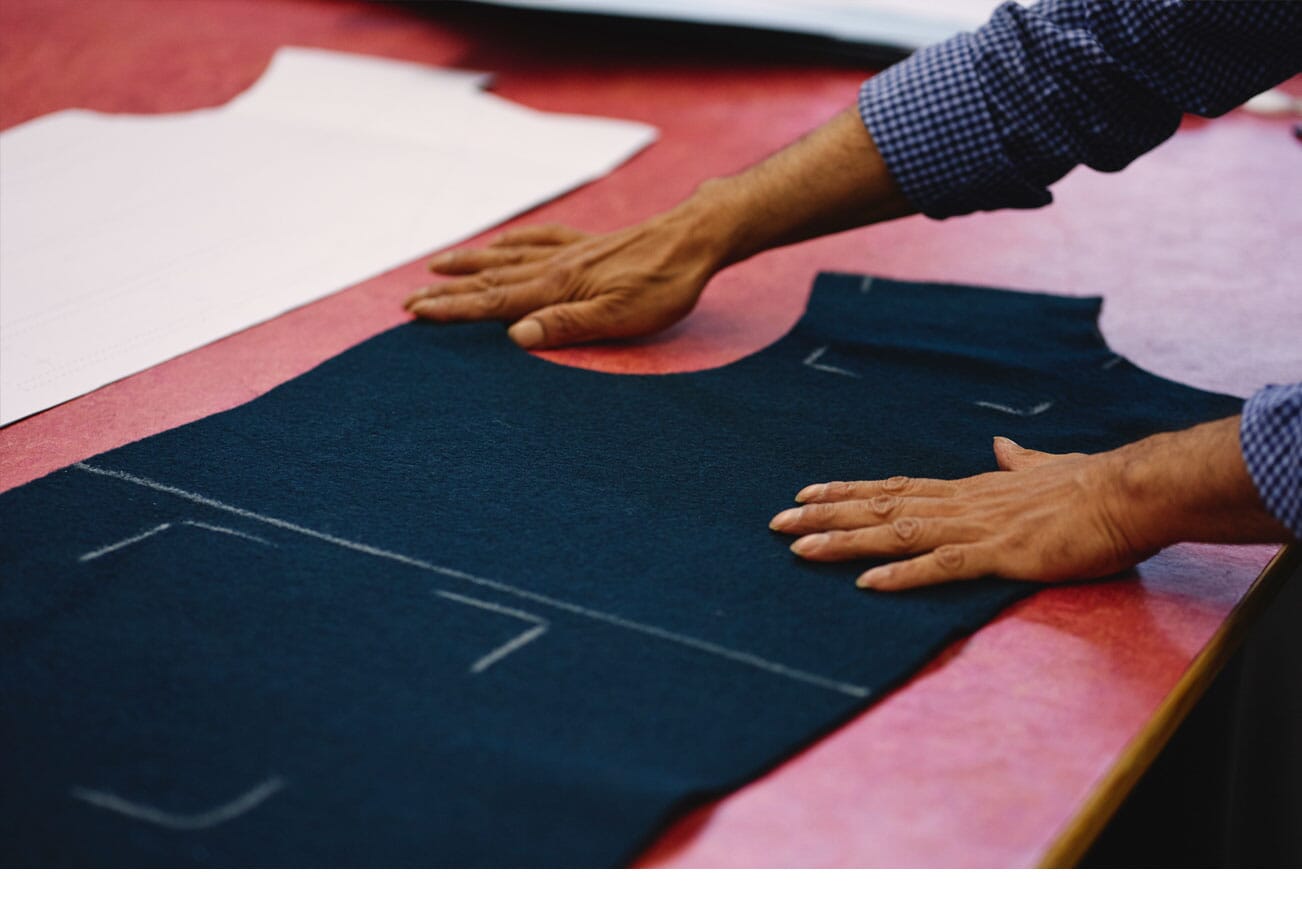
What are the first steps in the design process after you’ve found inspiration?
Sketching. We’ll sketch some ideas, source fabrics and trims and then we begin to narrow these down to make a full tech pack. Once this is made, we’ll send it to the pattern cutter and production team who at this point have everything needed to create the piece.
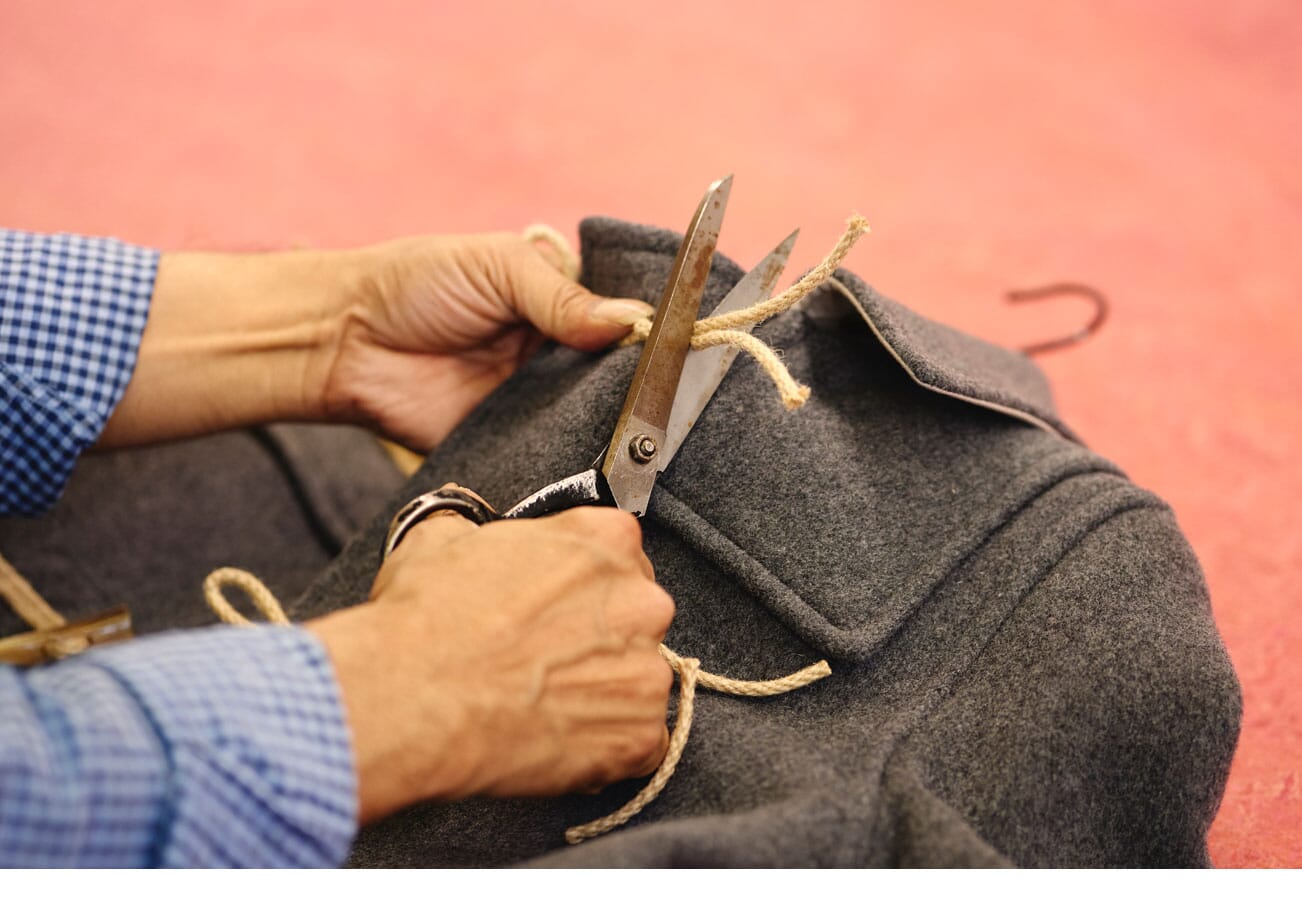
Where does the production process take place?
We make everything in the UK, from start to finish. We work roughly one year in advance to launching the product in stores as we sell at wholesale, which is done 6 months before it hits the stores.
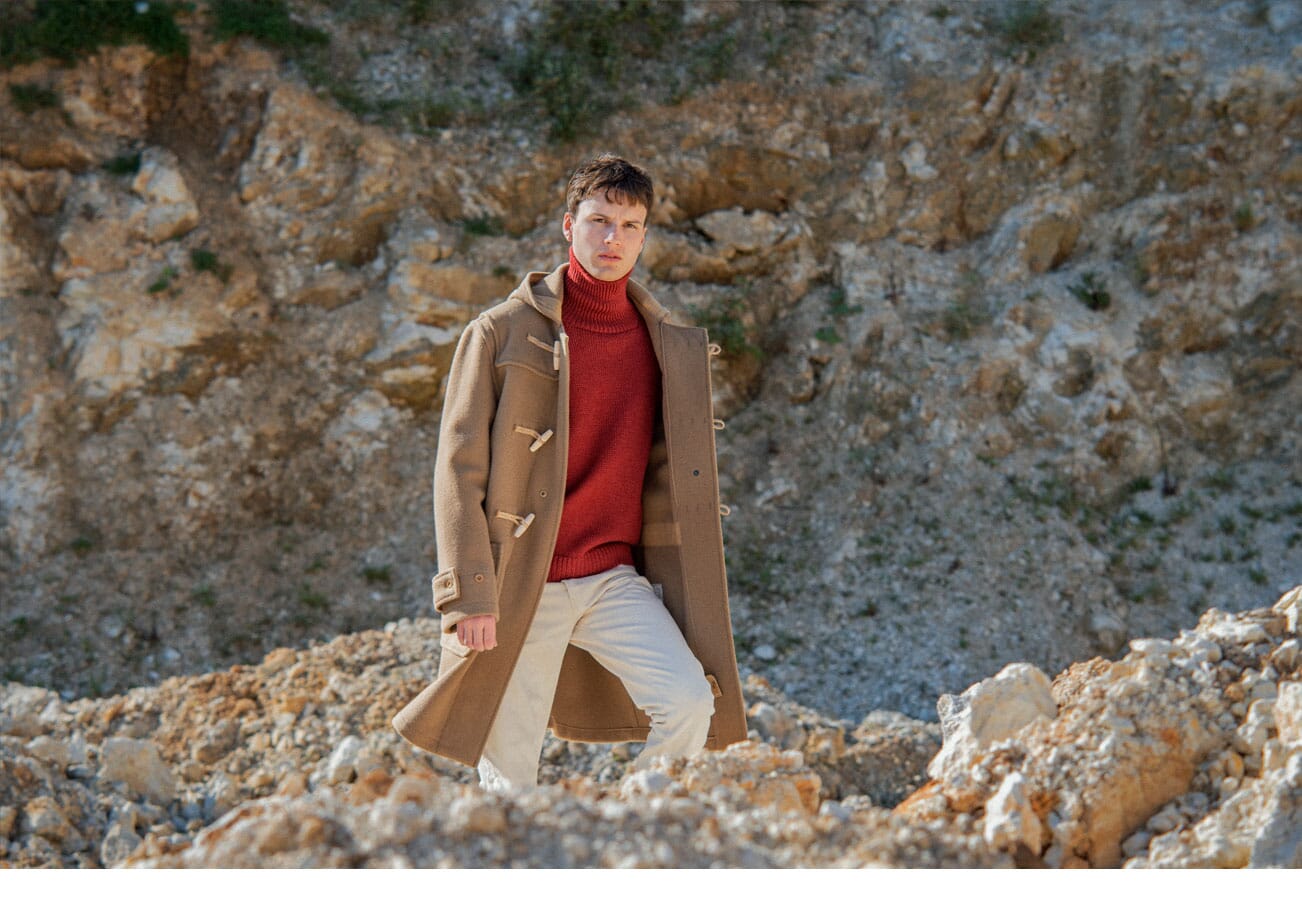
How long before you get your first samples?
Because all of the steps take place in the UK, we can turn around samples quite quickly. It’s usually within a month of sending off the tech pack. The fabric and trim take the most time to arrive, we expect them to take around 8 weeks as they’re sourced in Italy.
So, can you give us a quick rundown of who is involved at each step?
Our design team will create a sketch and then it’s up to them to source fabric and trim as they have the best idea of the look and feel they’re searching for. From there it will go to a pattern cutter, once the pattern is made our garment tech will have a look and pass this on to the factory. Once this has been talked over at the factory, an initial sample will be made. The whole team will get together to carry out a fit meeting where we look at the garment and see how it can be improved. Once we’ve decided, it’s back to the drawing board until we’re happy. This may happen two or three times over to get it right.
How long did it take to nail down your workflow? Is it still developing?
Luckily, there are two main selling seasons in a year so our workflow is given an inflexible deadline whether we like it or not. That said, we do try to improve each year on efficiency and workflow within those parameters.
Shop Gloverall at OPUMO.
Expecting rain? Look no further than another new brand at OPUMO: Rains.